Reinventing Plastic Waste: The Game-Changing Role of Pretreatment Technology in Recycling
- Share
- Issue Time
- Jan 10,2025
Summary
Effective recycling of plastic waste relies on cooperation and technological innovation.
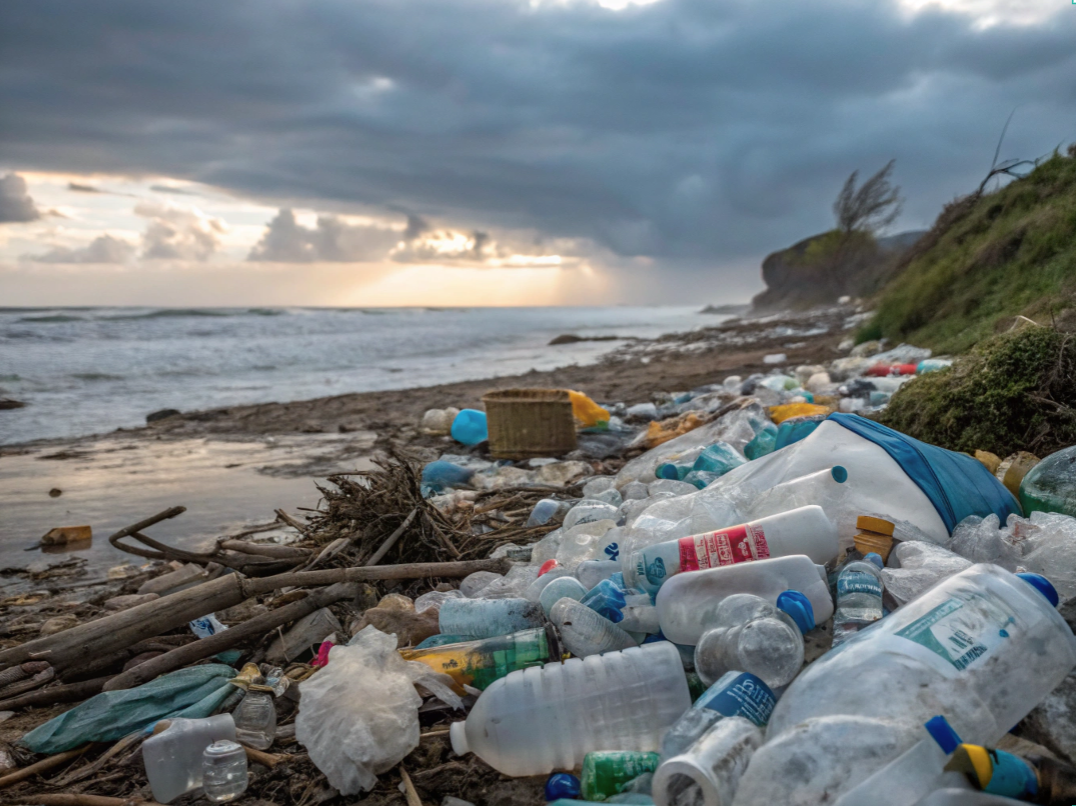
Plastic pollution has emerged as a significant challenge for the global environment. Annually, approximately 19 to 23 million tons of plastic waste enter aquatic ecosystems, heavily contaminating oceans, lakes, and rivers, and disrupting ecological balance. Since the 1950s, over 9.2 billion tons of plastic have been produced worldwide, with the majority ultimately becoming waste, either dumped in landfills or released into nature.
Due to their durability, plastics can take thousands of years or longer to decompose. As per the United Nations Environment Programme, plastic pollution is projected to rise in the upcoming decades, with plastic waste expected to triple by 2060, leading to alarming consequences for ecosystems and human health.
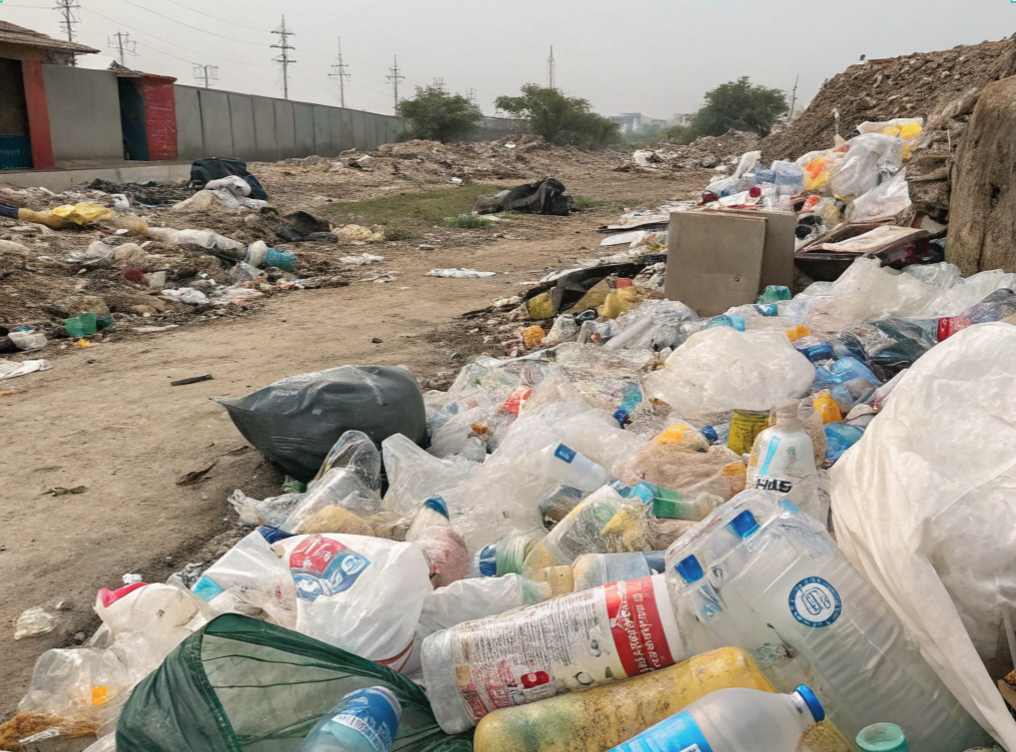
Plastic pollution poses a significant threat not only to the survival of plants and animals but also to human economic, health, and social well-being. Statistics indicate that the annual cost of addressing plastic pollution ranges from 300 billion to 600 billion dollars.
A considerable portion of plastic waste comes from disposable items like plastic bags, food packaging, and plastic bottles, which are major contributors to environmental pollution. More alarmingly, these single-use plastics are often discarded after their initial use, but they persist as microplastics, contaminating water sources and soil, which ultimately impacts ecosystems.
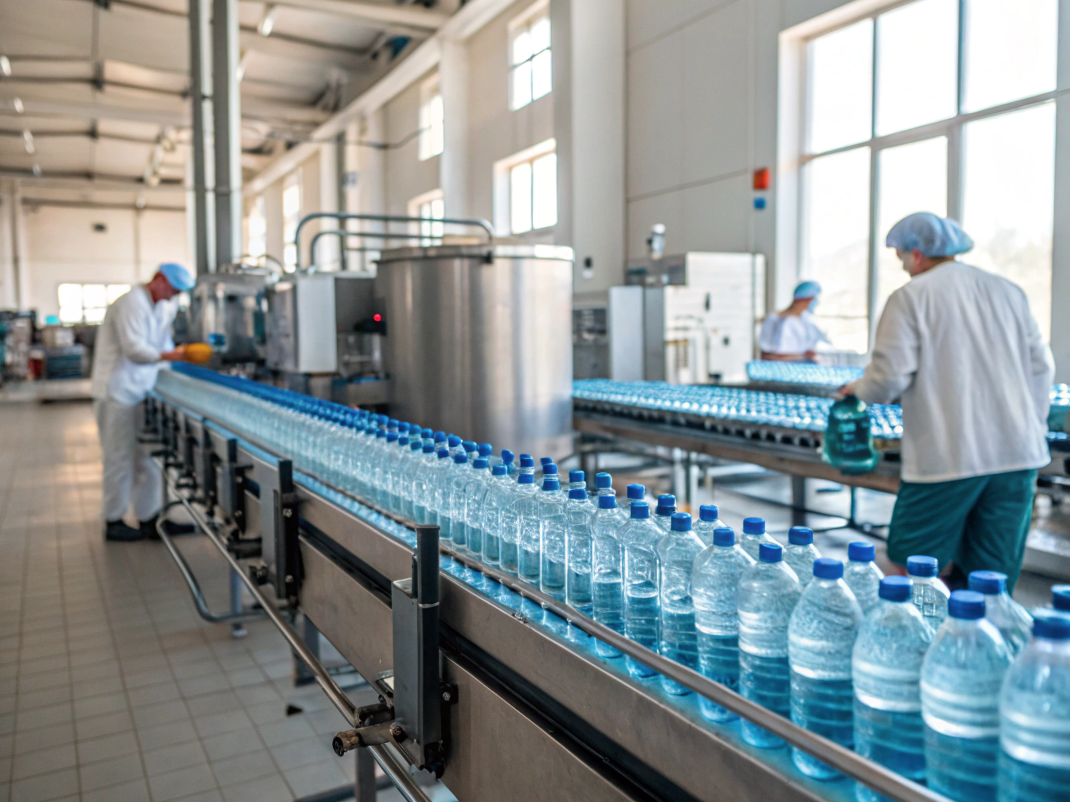
Principal Categories of Plastic Waste
Various types of plastic waste exist, with several major categories being particularly prevalent. These include polyethylene terephthalate (PET), high-density polyethylene (HDPE), low-density polyethylene (LDPE), polypropylene (PP), and polystyrene (PS). Approximately 500 billion PET beverage bottles are sold worldwide each year, with a significant portion ultimately discarded and finding their way into oceans.
Additionally, items such as plastic bags, cutlery, and food containers constitute significant sources of plastic waste. Microplastics, which consist of minuscule plastic fragments from numerous origins, including tire degradation, microbeads from personal care products, and plastic shards from synthetic turf, also pose a major concern. Given their difficulty to degrade in the natural environment, the harmful effects of these plastics on ecosystems are escalating each year.
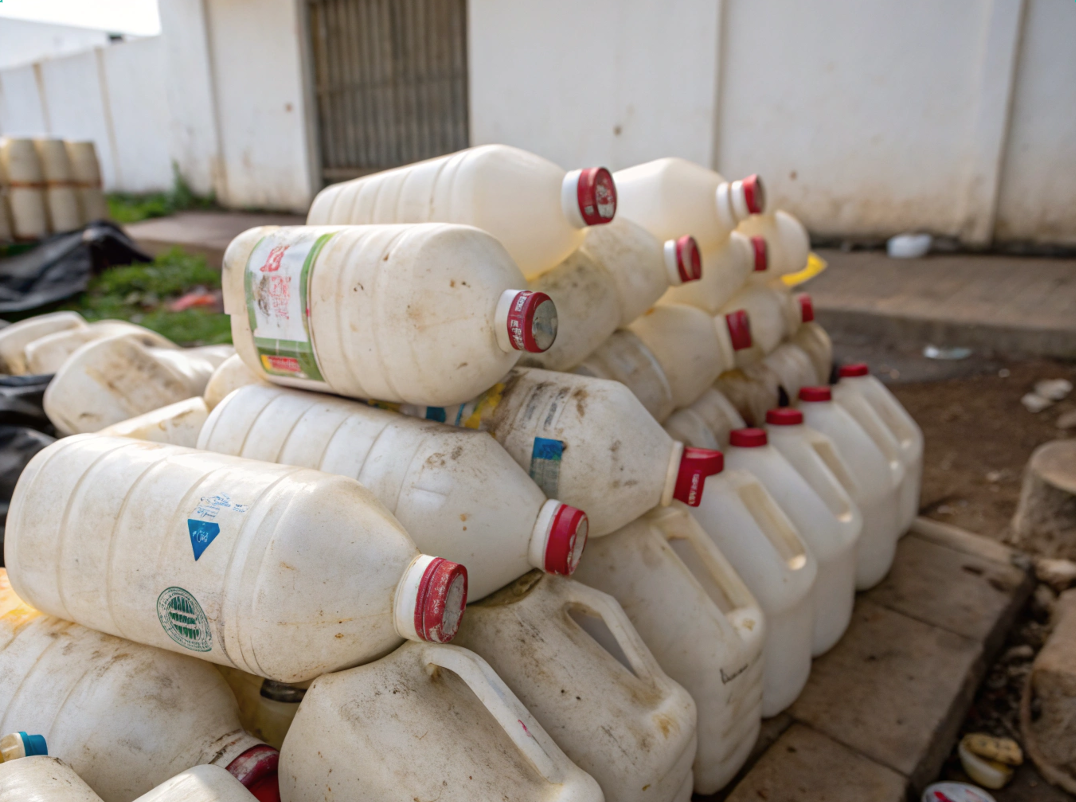
Mechanical Recovery Techniques
Mechanical recycling involves transforming waste plastics into reusable raw materials through various processes, such as sorting, washing, crushing, screening, drying, and repelletizing. This method effectively retrieves plastic waste while maintaining its chemical structure, thereby preserving the material's properties and enabling repeated reuse.
The benefits of mechanical recycling include low energy consumption, cost-effectiveness, and operational simplicity, making it the leading method for plastic recycling today. By recycling plastics and converting them into new post-consumer resins (PCR), we can significantly decrease the resource consumption and carbon emissions associated with new plastic production. When compared to traditional plastic manufacturing, producing recycled plastics requires approximately 79% less energy and results in more than 67% lower greenhouse gas emissions for new products.
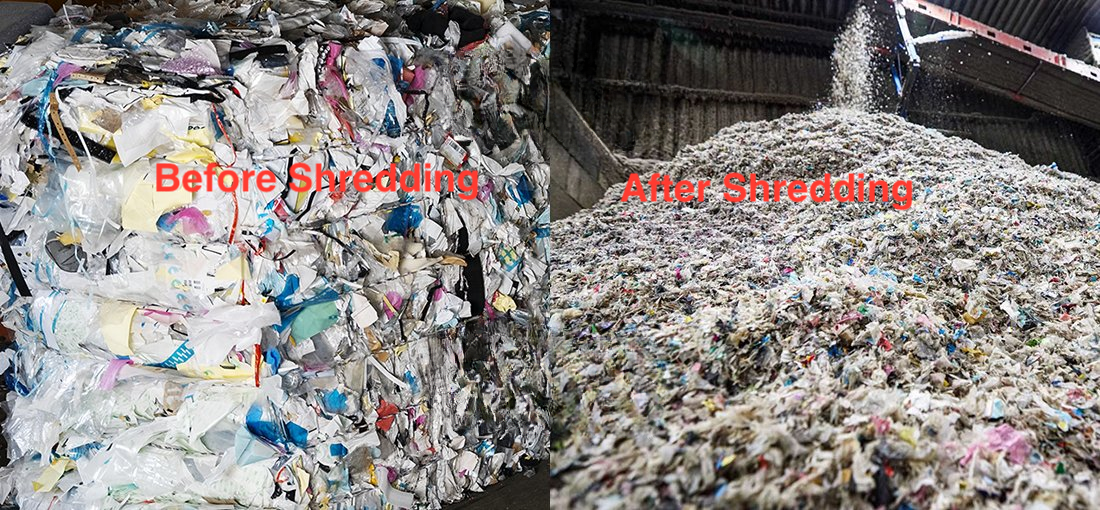
Harden's Recycling Pretreatment Technology
The pretreatment phase is a vital component of the mechanical recycling process, significantly influencing the overall effectiveness of recycling efforts. To achieve clean and high-quality recycled raw materials, waste plastics must undergo thorough fine crushing, washing, and separation to remove impurities.
With over a decade of expertise in solid waste resource processing, Harden Machinery has created a highly efficient single-shaft industrial plastics shredder capable of handling up to 200,000 tons of waste plastics per hour. The company's shredders feature several patented technologies, including intelligent built-in circular compression, gap shearing, and a close-row knife shaft design. These innovations ensure equipment stability, uniform crushing outcomes, and an impressive output capacity.
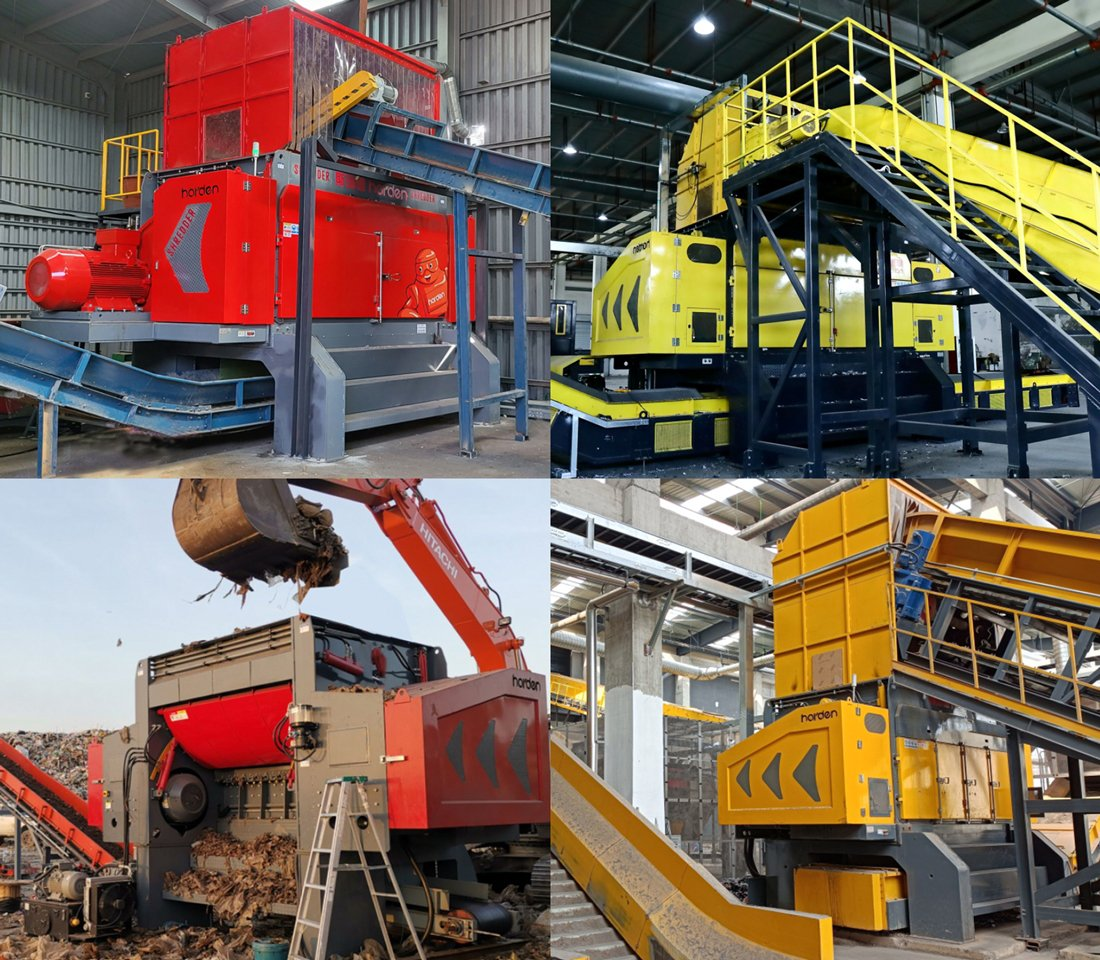
Harden Machinery offers tailored solutions for various types of waste plastics and the specific needs of different industries. Their equipment can be adjusted in terms of torque, speed, and knife configurations based on the characteristics of diverse materials, ensuring that the final recycled materials meet industry standards for further resource processing. As a result, Harden Machinery's recycling equipment has gained significant traction in the global market, establishing the company as a key player in the plastics recycling sector.
Plastic pollution presents a critical global challenge that requires immediate action. While recycling remains difficult, advancements have been achieved through methods such as mechanical recycling. Firms like Harden Machinery are improving recycling efficiency with innovative approaches. Successful plastic waste recycling depends on collaboration and technological advancements to safeguard the global environment.