Reimagining Waste Tires
- Share
- Issue Time
- Dec 13,2024
Summary
The piece emphasizes the value of recycling materials found in tires and introduces an efficient recycling system by Harden that optimizes the process.

As the global economy progresses, the demand for tires continues to rise. Each year, over 1 billion waste tires are generated worldwide, accounting for about 2% of total waste. This increase is primarily driven by the growing automobile sales in both developed and developing countries.
According to data from the U.S. Federal Highway Administration's Research and Technology Division, the United States produces approximately 280 million waste tires annually, averaging around one tire per person. Of these, close to 30 million tires are either reused or retreaded, leaving nearly 250 million tires that require proper management. Waste tires not only contribute to environmental pollution but also pose significant challenges for our circular economy. Thus, effective tire recycling and reuse are crucial to addressing these issues.
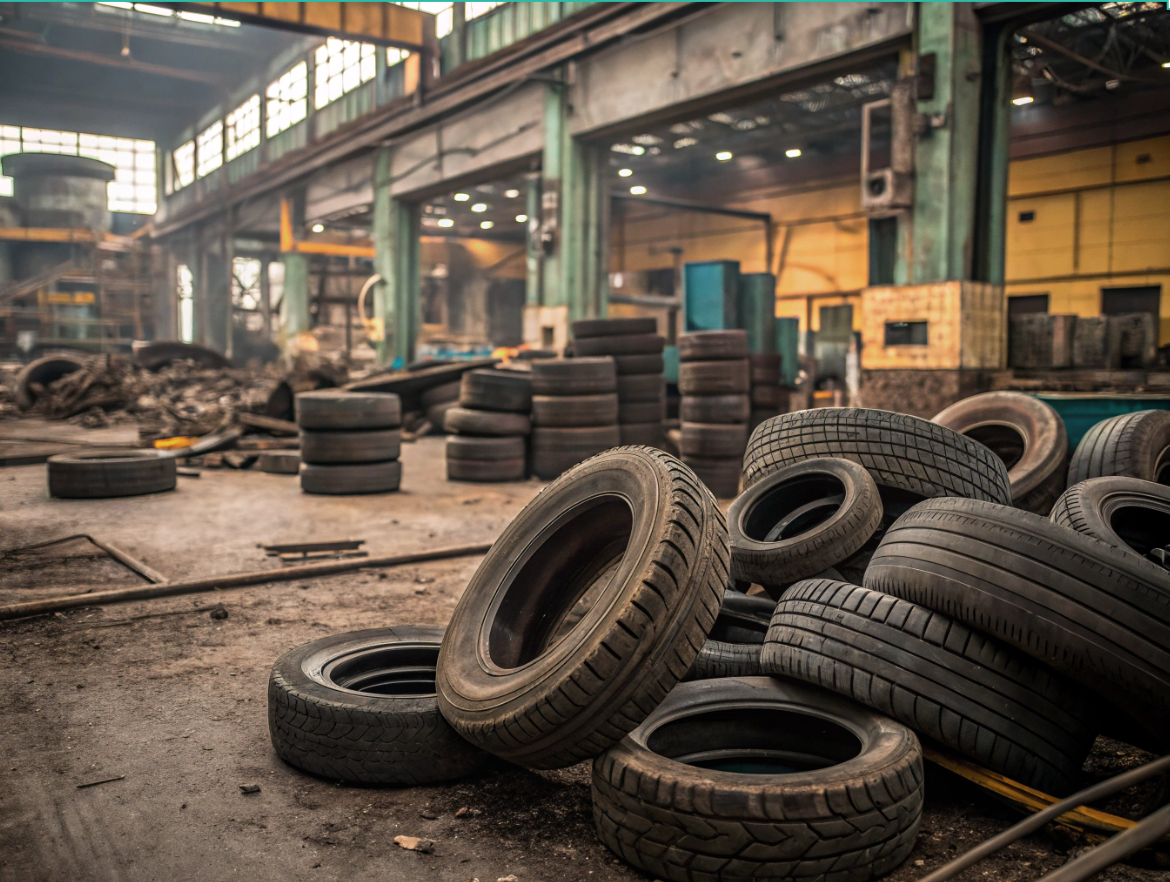
Various Methods for Tire Reuse
One prevalent strategy for managing waste tires is retreading, a process that involves replacing the worn tread with a new one. This technique successfully reuses about 90% of the tire's material, minimizing waste and enhancing safety. However, for those tires that cannot be retreaded, alternative disposal methods need to be explored.
Governments around the globe advocate for the recycling of waste tires, particularly those deemed unsuitable for retreading. A common recycling method includes removing the bead from the tire, cutting it, and processing it into products like shims or belts. By slicing tires into different sizes, we can expand recycling possibilities. Waste tires can be shredded into various sizes, generally categorized as shreds (50-300 mm), chips (10-50 mm), and granules (1-10 mm). The equipment needed will vary depending on the size range required for production.
Uses for Tire Shreds, Chips, and Granules
Tire shreds processed by machines such as the "Super Chopper" are ideal for transporting waste tires and possess a high calorific value, often used in the cement and paper industries as a supplement to traditional fossil fuels. Additionally, tire shreds can serve as Tire Derived Aggregate (TDA) in civil engineering applications, such as lightweight fill and vibration reduction.
Tire chips can be produced from whole tires or tire shreds using shredders equipped with built-in screens. They are applicable in the same TDF uses as tire shreds but offer the added benefit of lower steel content. Tire chips are also utilized in the equestrian industry, mixed with sand or sawdust to protect the legs of horses, especially in countries like the UK, where this is a significant industry.
Rubber granules can be used in the production of rubber mats and molded products, widely employed in sports facilities and artificial turf. Moreover, recent applications for rubber granules include pyrolysis, a process in which rubber is converted into oil and solid new materials or fuels.
Rubber granules can be used in the production of rubber mats and molded products, widely employed in sports facilities and artificial turf. Moreover, recent applications for rubber granules include pyrolysis, a process in which rubber is converted into oil and solid new materials or fuels.
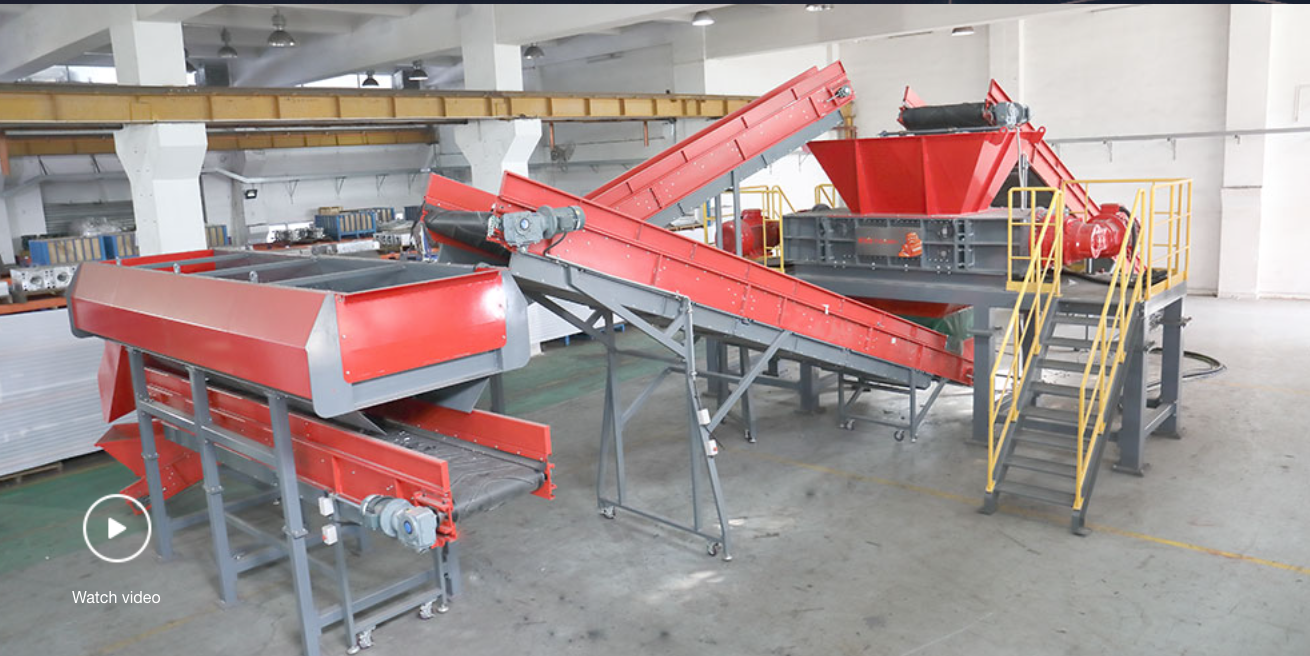
Recycling Metal and Textiles from Waste Tires
Waste tires contain around 20% steel and 10% textile material. The recovered steel holds significant value, as steel manufacturers globally often recycle this material from tire recycling plants, offering attractive prices, especially when it has been stripped of rubber and textile residues. Conversely, the recycled textile is usually incinerated due to its high calorific value, making it a beneficial additive in the cement industry.
Effective Tire Recycling Solutions
To tackle the challenges associated with waste tire reclamation, Harden provides a complete and effective tire recycling system. This system is designed with a modular approach, featuring low noise levels, minimal energy consumption, high throughput, and a consistent discharge particle size.
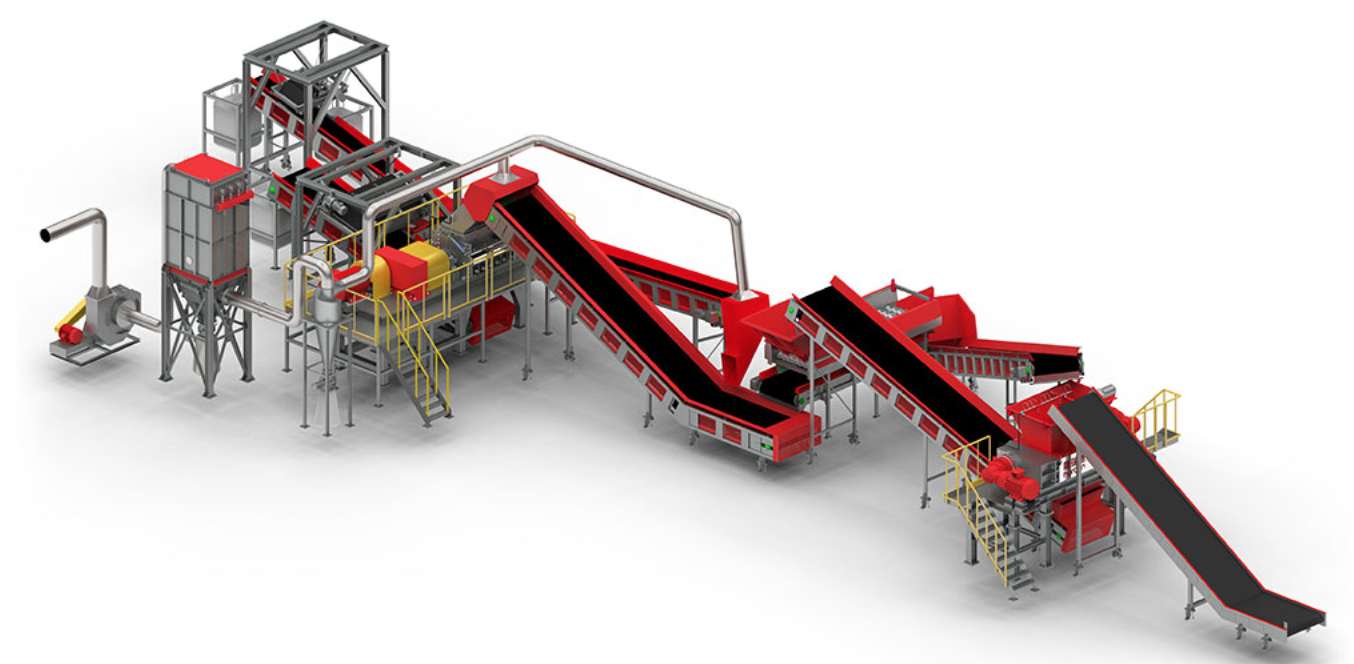
In this system, waste tires are introduced onto a conveyor belt that feeds into a double-shaft shredder for processing. The resultant tire shreds are sorted by a disc screen to ensure size control. Shreds that do not meet the specified size criteria are sent back to the shredder for further shredding until the desired size is obtained. Ultimately, the system produces high-quality tire-derived fuel (TDF), facilitating effective recycling of resources.