Reuse of Waste Textile: Pretreatment Technology Reveal!
- Share
- Issue Time
- Dec 3,2024
Summary
There are three main methods to achieve waste textile reuse: Physical recycling, chemical recycling, RDF alternative fuel (energy recovery). Among these, the waste pre-shredding process is the key point.
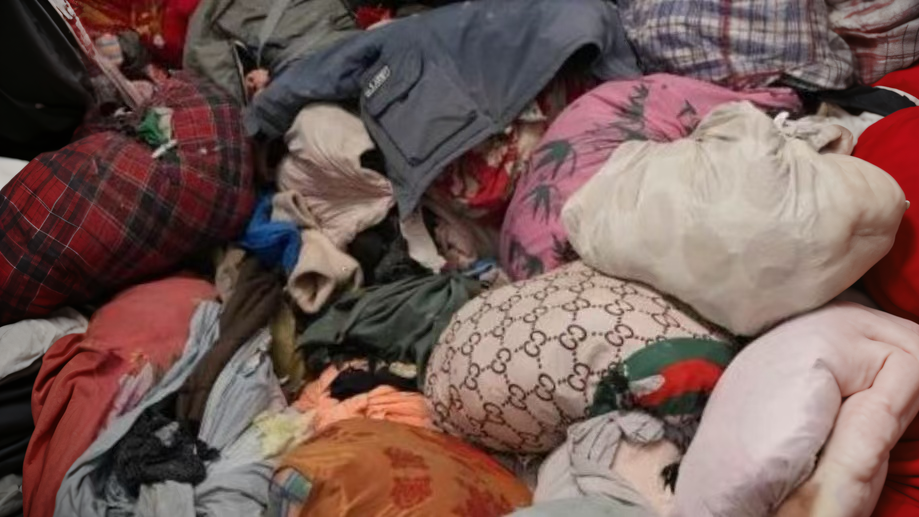
The Technical Difficulties in Waste Textile Reuse
There are three main methods to achieve waste textile reuse: Physical recycling, chemical recycling, RDF alternative fuel (energy recovery). Among these, the waste pre-shredding process is the key point.

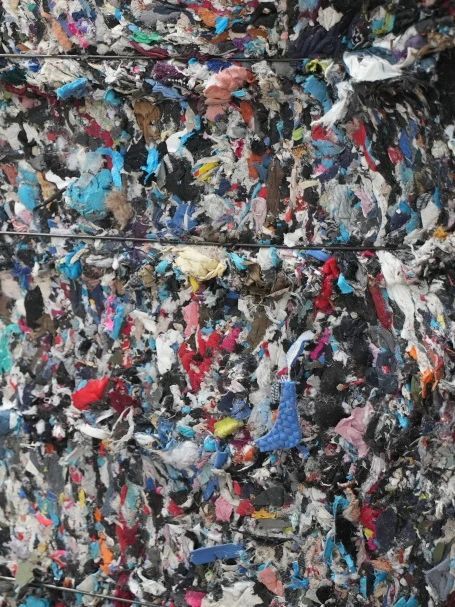
Waste textiles that have not been shredded are often larger in size and irregular in shape, which brings a lot of inconvenience to subsequent recycling steps.
For instance, when the fiber is separated, chemically processed, or reprocessed into new products, the waste textile in large size cannot take part in the above processes, which finally causes low efficiency and not ideal recycling rate.
Moreover, during the process of RDF preparation, large-sized waste textiles cannot be completely burned in industrial kilns, resulting in a large amount of heat energy loss.
Thus, it is necessary to turn the waste textile into smaller, more even waste through the process of fine shredding.
Focus on waste textile shredding tool: Single-shaft Shredder
In the process of waste textile reuse, the most common pre-shredding way is shear crushing. It is similar to some shearing machines with rotating blades. When the machine is running, the blades move staggered with each other, cutting the textile into pieces like scissors.
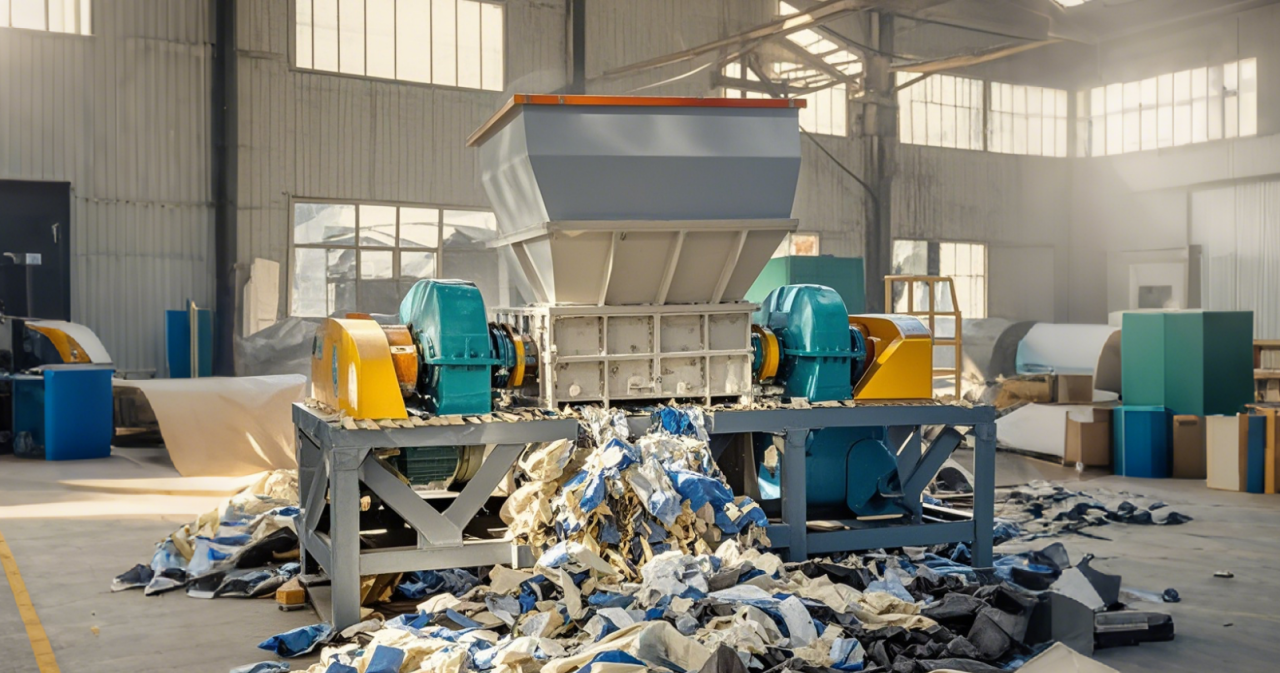
However, the traditional shear crusher has low crushing efficiency, is easily blocked by entangled materials, and the discharge is not uniform, which has become an obstacle that limits the large-scale development of waste textile reuse.
Harden Machinery Ltd. began to develop solid waste resource treatment technology in 2012. Over more than ten years of in-depth market analysis and crushing experiments, it independently developed a fine crushing tool - a single-shaft crusher.
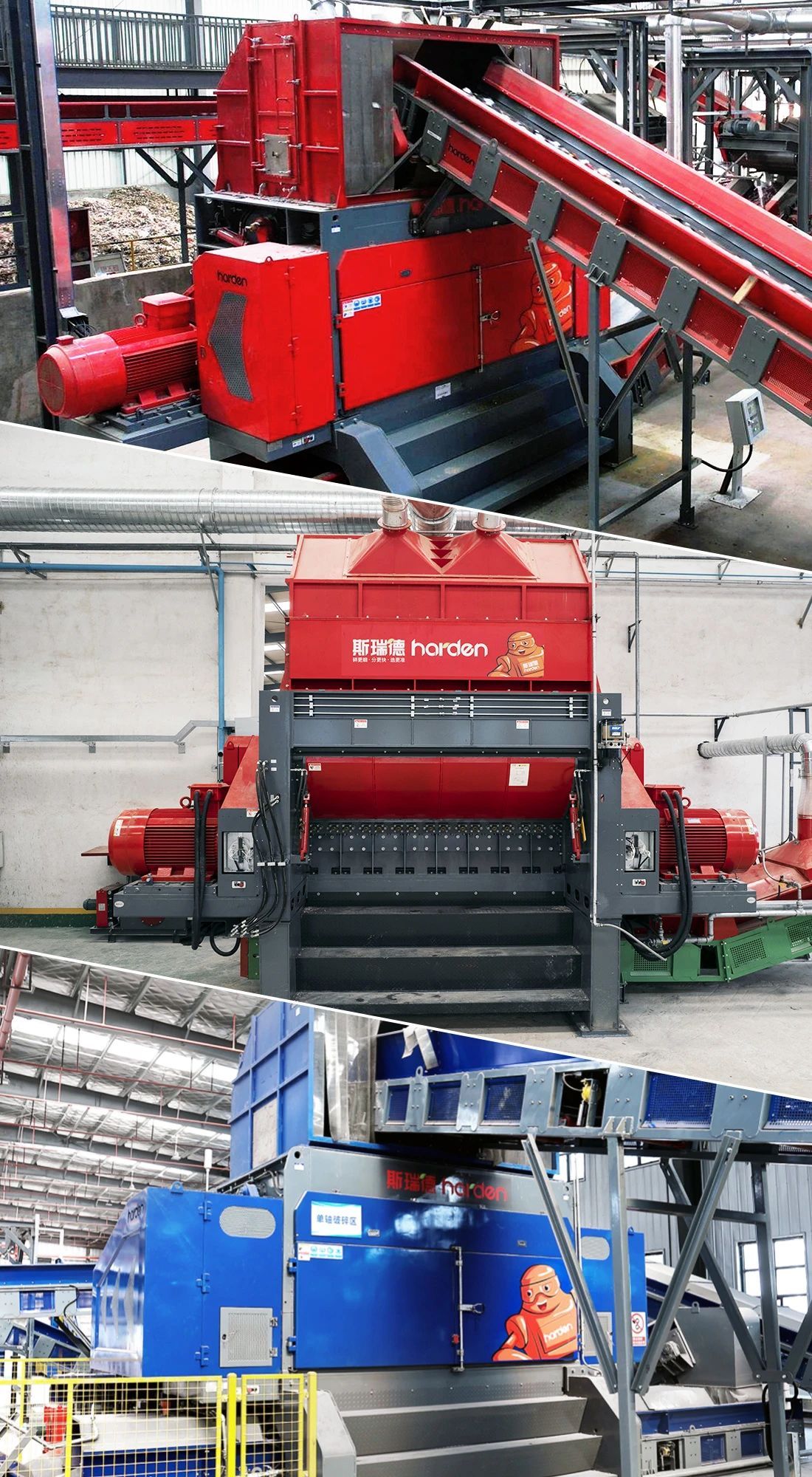
It adopts more advanced close-packed blade cutting technology, which increases the shearing efficiency by 50%; the uniquely designed blades and screens, coupled with the efficient counter shaft + large flywheel variable frequency drive system, increase the final crushing output size Finer, more uniform, higher yield.
Waste Textile RDF Processing System
According to the characteristics of waste textiles and the emerging demand in the textile waste energy recycle markets, Harden has developed a waste textile RDF preparation system.
Through the combination of modular and integrated equipment, and fine processing processes such as "crushing + air separation + magnetic separation", the metal and impurities in the waste textiles are separated, and finally finely crushed into RDF alternative fuels of 30-100mm size.
The high-value RDF and low carbon emission are favored by coal-fired enterprises such as power plants and cement plants.
Solid waste fuel data in 2023 shows that every 1.5 tons of RDF alternative fuel used can reduce the use of 1 ton of raw coal, thereby saving hundreds of dollars and reducing 2.25 tons of CO2 emissions.
RDF alternative fuel preparation technology is applicable to all waste textiles and does not limit any fiber material.
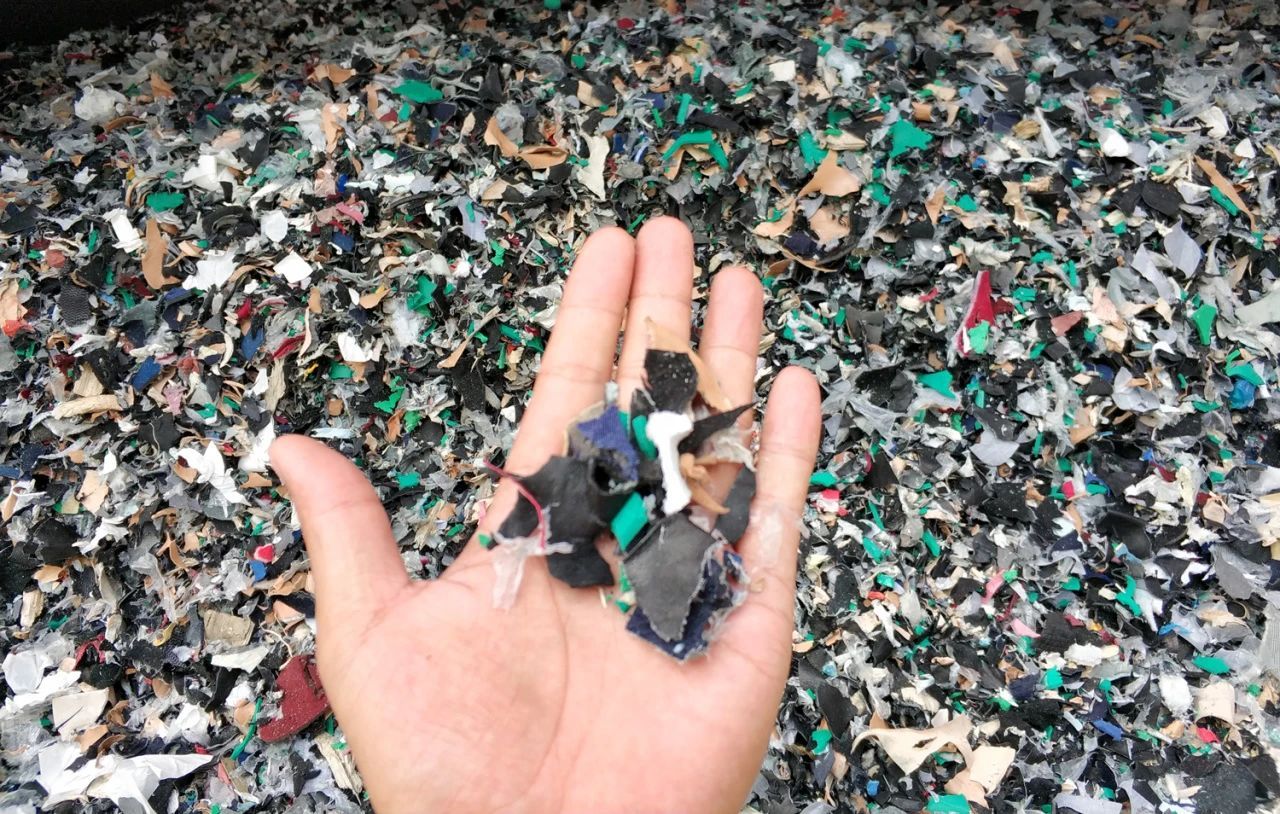
The process is simpler and more convenient than chemical recycling and physical recycling. In the future, it may become the preferred method for recycling, harmlessness, and volume reduction of waste textiles.